轧辊检测原理及应用_火焰检测原理及应用
轧辊检测原理及应用由刀豆文库小编整理,希望给你工作、学习、生活带来方便,猜你可能喜欢“火焰检测原理及应用”。
第六章 轧辊检测
无损探伤发展至今,已被轧辊制造者和轧钢厂用来评判轧辊材料的质量。作为轧辊维护的一个常规项目,无损检测的目的是发现最早期的轧辊问题,并防止未采取改进措施的轧辊再次上机使用。轧钢厂常用的方法是涡流、表面波、渗透、酸侵、磁粉、和硬度检测。最快速、准确、可靠的检测技术是涡流和超声波检测。它们同时使用时,所有对轧辊及轧制产品不利的表面情况都能100%的准确检出(表1)。渗透、酸侵具有花费不多的优点,然而它们耗时长,不是100%的可靠。因此它们应与涡流和超声波配合使用。
表1 检测方法
超声波
有效
径向深度(1)热损伤/软点 表面微裂纹 <0.006″ 表面微裂纹 >0.006″ 次表层缺陷 残余磁性 加工硬化
涡流
表面(2)双晶斜探头
0-0.003″
▲
▲
▲ ▲
0-0.050″
▲ ▲
0-6″
▲
直探头
0.5″-
▲
(1)设备参数的功能(频率、晶体类型、探头形状)
87(2)圆周方向(要求扫描3次)轴向(要求扫描2次)
一、涡流探伤
涡流探伤是轧辊磨削之后,确定缺陷位置如软化区(热损伤)、宏观裂纹和磁化的一种方法。磨床上,一个双线差分探头放置在辊身一端,靠近辊面处,随着轧辊以设定的速度转动,探头慢慢移动跨过整个辊身长度。探头移动速度和轧辊转速的同步性是设定好的,以确保辊面的每一点都通过探头。随着探头在辊身移动,在交流电流的作用下线圈间的辊面上产生涡流。线圈间电流的导电性和路径长度的瞬间变化都能被检测出来,并显示在两个独立的频道。一个称为压伤/热损伤频道,一个称为裂纹/剥落频道。涡流探伤的特殊步骤取决于使用的涡流设备,由设备生产者提供。导电率的变化可在压伤/热损伤频道上检出。它是辊面相邻点间的硬度和显微组织变化的结果。磁化区内所有相邻点间也会引起导电率的连续变化。高斯通量可用来证实剩余磁性的存在。(大于30Gau)。能引起辊面上导电性反复变化的一般条件包括(但不限于此)局部超温、局部工作硬化、表面粗化和外来夹杂物嵌入辊面。这些情况在压伤/热损伤频道表现为超过噪音水平的单独的波峰或超过噪音水平的大面积的草状波峰(图2)。
在裂纹/剥落频道可检出路径长度的变化,这个变化是表面裂纹引起的。当探头通过一个裂纹上方,感应电流必定沿裂纹壁向下流动并到达裂纹的另一侧形成环路。路径长度的不同以一个独特的脉冲峰显示在裂纹/剥落频道(图2)涡流探伤不能检出小于0.006”宽的裂纹。宽度大于0.006”的裂纹只有一半的准确率。为了所有表面裂纹能准确检出,应使用超声波探伤。
图1 磨削操作完成后,进行涡流探伤。
图2 涡流探伤记录表
大箭头指头指示辊面上的典型的热损伤。小箭头指头指示压伤/热损伤频道的多余噪音。中箭头指头指示裂纹/剥落频道上显示的裂纹。
二、表面波探伤
表面波超生波探伤使用一个固定在直角楔形块上传感器,十分准确地检出表面裂纹。表面波发射圆周方向的高频声波,检查反射或吸收的声波情况。轧辊内部所有界面都会一定程度的反射或散射声波,包括裂纹、夹杂、晶界和其它不连续因素。金属—空气界面(裂纹)反射大部分声波,而金属—固体界面(夹杂)反射小部分声波。被反射的声波随后返回到传感器的测试屏幕上,显示一个波峰。以下是进行表面波超声波检测的一个基本过程:
1.0应用以底面回波为基础的接触法超声波技术(参看ASTMA388)1.1超声波设备
1用脉冲型超声波仪器产生和显示超声波信号。
2使用压电晶片材料的探头,用来发射和接收超声波信号。1.1.3一根带有配套接头的同轴电缆连接超声波设备和探头。
1.1.4使用偶合剂以便在锻钢辊上有效地发射、接收超声波信号。一般为油、甘油或水。1.2.超声波检测 1.2.1周向表面检测
该检测的目的是检查轴向表面和浅次表层缺陷。1.2.2轴向表面检测
该检测的目的是检查横截面表面和浅次表层缺陷。
1.3周向表面检测 1.3.1探头
使用2.25MHz,0.5″×1.0″的有机玻璃的直角楔形探头发射超声波。
1.3.2准备轧辊
把轧辊放在支架上,避免支架与辊身接触。如果必要用溶剂请洗并用布擦干。
1.3.3施加偶合剂
在辊身上部,沿辊身全长涂刷一条薄而透明的偶合剂带。1.3.4设置、显示和灵敏度
在一个没有相关缺陷的区域进行设置。设置市时基线表示一个大于辊身周长1/2的距离,时基线上的始波在屏幕的最左边。把探头放在偶合剂上并获得一个圆周方向的底波反射。调整增益(dB)使底波波高达100%fs,调整时基线把底波置于屏幕的最左边。(图1)。
1.3.5接触检测—辊身圆周方向第一个180°。
将探头放在辊身一端并把表面波对准圆周方向,沿偶合剂以小于8″/s移动探头,同时保持显示器屏幕100%的底波反射。确定和标记缺陷位置做好记录。1.3.6接触检测—辊身圆周方向第二个180°。
反转探头圆周方向位置重复1.3.5操作(图2)。1.4.7接触检测—端头区
擦去辊身的偶合剂,重新在辊身端面涂刷偶合剂,重复1.3.5和1.3.6的操作。
1.4 轴向表面检测——辊身 1.5.1探头
同1.3.1。1.4.2准备轧辊
同1.3.2。1.4.3施用偶合剂
在辊身驱动端环绕圆周(360°)涂刷一个薄的偶合剂带。注意如果轧辊的旋转机械不能使用应涂刷圆周的1/2(180°),改变轧辊位置并重复。1.4.4设置、显示和灵敏度
除设置的时基线表示一个大于辊身长度的距离外,其余同1.3.4。把探头放在偶合剂上获得一个长轴方向的底波(图1)。1.4.5接触检测—驱动端
将探头放在辊身驱动端并把表面波对准长轴方向,沿偶合剂以小于8″/s移动探头,同时保持显示器屏幕100%的底波反射。屏幕显示任何大于10%波高的缺陷。确定和标记缺陷位置,做好记录。1.4.6接触检测—操作端
擦去辊身的偶合剂,重复步骤1.4.3、1.4.4和1.4.5。
时基线
图 超声波探伤的显示屏幕
图2
周向表面检测
三、渗透探伤
渗透探伤可以随时进行(磨削后最常用)。它被用来显示轧辊表面裂纹,红色染料的渗透剂被用在轧辊表面。染料在表面张力的作用下,进入裂纹内表面,一段时间后,用清洁的干布擦干轧辊。在表面张力的反向作用下,染料从裂纹中反渗出来。显影剂喷洒到辊面裂纹就显现为白背景下的红线。深透探伤也可用荧光染料来做。这时荧光紫外线代替显影剂显示裂纹。渗透探伤对显示大而宽的裂纹是准确的。然而,如果裂纹太窄,渗透剂不能进入裂纹,显影剂就不能显示裂纹。一般地,最好在涡流探伤和超声波探伤确定表面缺陷方位后,只在有缺陷的区域内进行而不是整个辊身,进行此试验。
下面是使用红色深透剂方法,进行渗透探伤的简要过程:
·用超声波和涡流技术识别缺陷区域,近似的1/4圆周范围内。标注这个区域以便后续工作。
·用抹布擦去这1/4圆周上的过多油脂、灰尘等。
·拿一块抹布,向上面喷洒清洁剂(多喷一些)用这块湿布再擦一次,不要直接向轧辊喷清洁剂,这样会降低结果等级。
·手执容器距辊面大约8”远,向检测区域喷渗透剂(图1)。反复大量喷洒是有益的,但太多则会浪费。
·让渗透剂渗进轧辊至少10分钟(长一些更好)。
·用清洁的干布擦净轧辊下面多余的着色剂,定期更换清洁的抹布。以免弄脏染料。
·看到检测面见干后,向另一块抹布喷清洁剂。用湿布擦去剩余的红色染料。向上述一样定期更换抹布。
·手执容器距辊面大约8—10”远,向检测面喷显影剂,从一侧向另一侧均匀移动,使显影剂均匀。
·随着显影剂开始干燥,红线将显现,显示任何存在的宏观裂纹(图4)。如果没有线出现,那么检测区域就没有宏观裂纹存在。
·估算裂纹尺寸大小,确定恰当的补救方法(磨削、、车削、手工打磨,等)。
图1
在辊身可疑区使用深透剂
图2
几分钟后擦去深透剂
图3 在辊身可疑区使用显影剂
图4 渗透探伤发现宏观裂纹。红线指示裂纹位置。
四、酸侵检测
酸侵检测可以随时进行(最常见的是在磨削加工后)。被用来显示轧辊表面裂纹和硬度变化等情况。当酸作用在辊面较软的区域将“烧伤”或“变黑”。相对较硬的区域侵蚀速度较快并留下不同的酸侵外观。酸侵也能检测裂纹。酸侵蚀时,侵蚀剂在表面张力的作用下进入裂纹,当表面酸液被擦净后,裂纹中的剩余酸液渗出,烧伤周围区域,裂纹便被显现出来。酸侵检测在先是热损伤、宽而大裂纹方面是准确的。然而,如果裂纹太窄,酸液不能进入裂纹,裂纹也就不能显现出来。一般地,最好在涡流探伤和超声波探伤确定表面缺陷方位后,只在有缺陷的区域内进行而不是整个辊身,进行此试验。下面是酸侵检测的简要过程:
·打磨、清洗、吹干要做酸侵的辊面,确保辊面无任何镀层(铬)和任何轧制表面的氧化层。
·用棉球蘸20%Nital侵蚀剂擦拭酸侵面至少1.5分钟(图1)。不要让酸侵面变干。
·用甲酸充分冲洗侵蚀剂,与此同时用另一块棉球擦净酸侵面上的沉淀物。·用压缩空气吹干酸侵面。
·软或硬的区域显示不同的明暗程度。在酸侵面上和周围金属间软区显得较黑,硬区显得较亮。
图1 用20%Nital侵蚀辊身的一个区域。
图2 用脱脂棉、甲醇擦拭酸侵面。
图3 用不含水分的压缩空气吹干酸侵面。
图4 经酸侵发现一个软点(热损伤)在酸侵表面热损伤表现为较黑的区。
五、磁粉探伤
磁粉探伤可以在任何时间进行。主要用来检测辊颈上的裂纹。辊颈部分的裂纹一般是圆周方向、位于圆弧处。这里所讨论的磁粉探伤不能用在辊身表面。因为所使用的磁场强度能使表面磁化,影响轧制产品的质量。这个检测通过在备检面的中部激发轴向的两磁极间的磁场来进行。细微的磁粉轻轻的吹过两磁极间的辊面,两磁极间的任何界面都起作用,改变磁场形状吸引细的磁粉显示裂纹。磁粉
探伤在显示大而宽的裂纹方面是准确的。然而,如果裂纹太窄,只有很少的磁粉被吸进界面,裂纹则显示不出来。下面是磁粉探伤检测的简要过程:
·用溶剂擦去油、灰尘等,清洁辊颈要做检测的部位。·把电磁轭的两个极沿长轴方向放置在辊颈要检测的部位上。·启动电磁轭产生覆盖被检部位的磁场。
·当磁轭带电时,一手拿容器罐小心均匀地挤压球形罐,向轭下施加磁粉。·绕被检面圆周方向移动磁轭并继续施加磁粉。·当磁粉吸附于界面时,裂纹就显示成磁粉细线。
图1 轧辊肩部圆弧处进行磁粉探伤
六、硬度检测
硬度检测应在磨削前后进行。它用来决定轧辊的整体硬度。也验证局部硬度的差异(热损伤、加工硬化等)。硬度检测的一般方法包括压痕(洛氏、维氏)和弹跳(里氏、肖氏)—参看图1-8。轧钢厂一般不使用洛氏硬度,原因是为了
保证检测精确,需要特殊的表面并且准备时间长。里氏和肖氏是最常用的硬度检测方法。弹跳检测通过坠落一个小冲击装置或冲头到辊面,测量弹跳的高度(肖氏)或速度(里氏)检测可以在任何洁净的表面上进行。并可反复多次以获得被检面上的平均硬度。
图1 在辊身上进行洛氏硬度检测
图2
在辊身上进行维氏硬度检测
图3 里氏硬度计(HLD和HLE两种冲头)
图4 肖氏HSD硬度计
图6 在辊身上进行肖氏HSD硬度检测
图7
肖氏HSC硬度计
图8
在辊身上进行肖氏HSC硬度检测
压力容器无损检测技术的原理及应用 [论文摘要]介绍当前压力容器制造和使用过程中所采用的无损检测技术,包括射线、超声、磁粉、渗透等常规技术和声发射、磁记忆等新技术,并论......
防雷器在电源系统中原理以及应用一、雷电防护基本原理雷电及其它强干扰对通信系统的致损及由此引起的后里是严重的,雷电防护将成为必需。雷电由高能的低频成份与极具渗透 性......
压力传感器原理及应用压力传感器是工业实践中最为常用的一种传感器,其广泛应用于各种工业自控环境,涉及水利水电、铁路交通、智能建筑、生产自控、航空航天、军工、石化、油井......
《PLC原理及应用》课程设计任务书 MITSUBISHI(三菱) PLC D组一、全自动洗衣机梯形图控制程序的设计与调试 1.控制要求:按下启动按扭及水位选择开关, 注水直到高(中、低)水位,关水......
传感器原理及检测技术(工程硕士)考试题1、简要说明非电量电测法的基本思想。2、简要说明传感元件与敏感元件的作用及区别。3、简述现代测量系统由那几部分组成及各部分的功能......
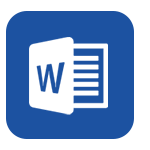